20% less process time - Sanner optimizes in VR
New Technologies for special products
Special products require special development measures. In the medical technology sector, things have to move fast – from the first idea to industrialization. Virtual Reality (VR) can help make processes more efficient. But how exactly? Sanner, item, and Halocline demonstrate this in a joint project.
Challenges in Medical Technology
Every step must be precise when manufacturing medical products. All assembly tasks are subject to strict regulations to meet the highest quality standards.
As a CDMO expert, Sanner GmbH develops plastic components for medical technology on behalf of its customers and supports pharmaceutical companies throughout the entire product development process – from concept to production and mass manufacturing.
A current project focuses on a drug delivery system. The challenges:
- Complex assemblies with multiple chambers and chips
- Maximum precision in assembly needed
- Short industrialization phase
To handle all this efficiently, the partners rely on a new strategy.
Three Partners, One Goal: Boosting Efficiency
The industrialization phase must be fast – from initial development to serial production, there’s little time. At the same time, high standards must be maintained:
- Cleanroom production in accordance with GMP guidelines
- Fulfillment of ESD requirements according to DIN EN 61340-5-1
- Flexibility to respond to customer requirements
The Solution: Virtual Assembly Planning with VR
With Halocline’s VR software, assembly workstations can be tested and optimized in a realistic environment as early as the development phase. Together with item and Sanner, Halocline creates the ideal conditions for a fast and secure project implementation.
Experience instead of imagining
Thanks to VR, production planning becomes easier to understand:
- 3D data is imported into Halocline
- The assembly table from item is displayed virtually
- Project teams realistically test processes in VR
Instead of merely imagining processes based on drawings, everyone involved can step into the digital workspace using a VR headset. There, assembly processes can be intuitively tested and optimized – long before any physical setup begins.
The Benefits of VR in Assembly Planning
- Detect errors early and avoid costly changes
- No physical mock-ups needed – faster planning
- Lower costs through digital adjustments
- Precisely validate process times
- Test and optimize ergonomics
With VR, the actual feasibility of the assembly process can be ensured. Every single step is reviewed for ergonomics, efficiency, and completeness – resulting in a safe and validated workflow.
Ergonomic and Efficient: Making Work Easier for Assemblers
VR also brings clear benefits for the people doing the work:
- Early ergonomic testing to create healthy workspaces
- Optimize processes in VR before the real workstation is built
- Personalize and improve workflows for more efficient tasks
If the team sees during the VR tryout that a movement is bad for joints or the back – no problem! The steps can be changed in VR until everything fits just right.
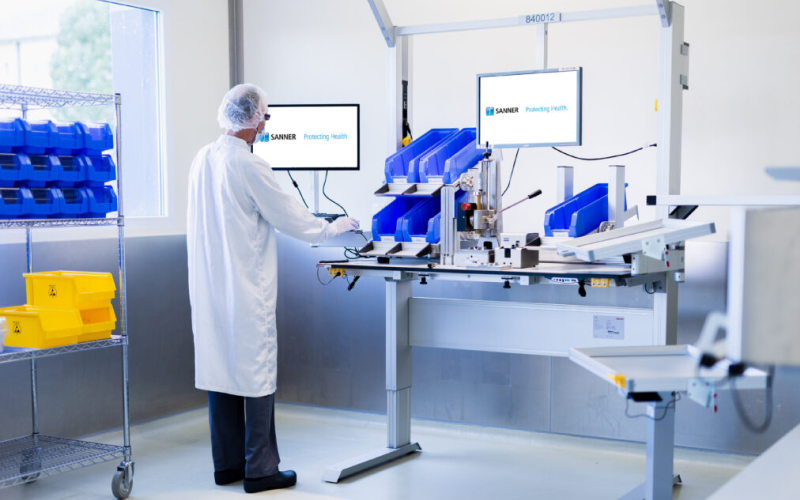
Designing efficient workstations with item
A key part of the solution is the workstation system from item. Its modular design lets teams create custom-fit assembly workstations – from structure to ergonomics to automation.
Thanks to the mix of item components and VR planning, companies benefit from:
- Flexible and customizable workstation setups
- Ergonomically optimized work areas
- Fast implementation with pre-configured modules
The assembly tables tested in VR are later built using item’s profile technology and connectors. This ensures that the virtual plan can be turned into a real workstation with precision.
From VR to Reality
After the first VR test, the results are added to the 3D concept and tested again. Only when everything works perfectly does the next phase begin:
- Finalize the virtual concept
- Get an offer for the real workstation (within one week)
- Build and review the workstation with the customer
- Start the pilot production
The teamwork between Sanner, item, and Halocline shows: With VR, process times can be reduced by up to 20% – a real game changer for the manufacturing industry.